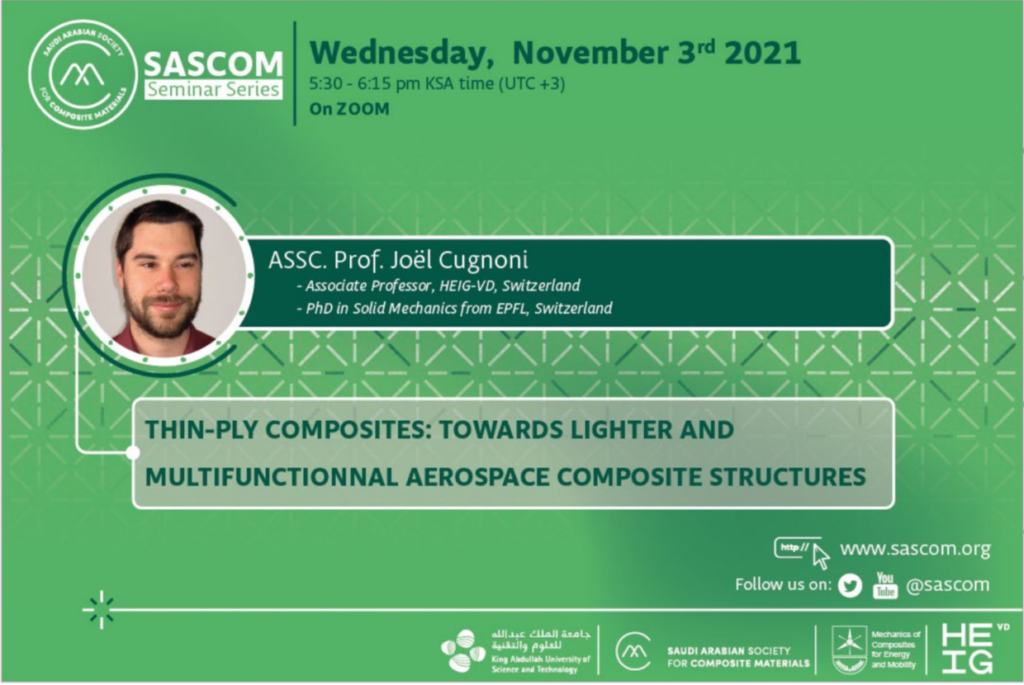
Wednesday, November 3, 2021
5:30 – 6:15 p.m. (AST)
On Zoom
Thin-Ply Composites: Towards Lighter and Multifunctional Aerospace Composite Structures
By Professor Joël Cugnoni , Associate Professor, HEIG-VD, Switzerland
Abstract
In recent years important progress has been made in the development of composite laminates using thinner pre-impregnated plies down to about 20 micrometers instead of ~200 micrometers for traditional composites. The motivation for this trend towards the development of thin-ply composites is not only to allow the production of thinner and lighter laminates for lightweight structures, but also to provide enhanced effective design space for laminate optimization as well as improved strength and damage resistance thanks to positive size effects.
The first prime benefit of using thinner plies is the ability to optimize among a larger number of ply orientations for a given laminate thickness or to allow the manufacturing of ultra-thin laminate, for example, for flexible structures or skins for lightweight sandwich panels.
The second benefit is that thin-ply composites present a very significant performance advantage over traditional composites due to delayed delamination and transverse cracking. Indeed, it has been shown that multi-axial laminates made of thin ply composites can reach an ultimate strength and first ply failure close to the ultimate strain of the fiber.
Thirdly, as it will be presented in this talk, thin-ply composites are also ideally suited to develop multifunctional structures that integrate electronic circuits to interconnect active components such as radio communication, sensors for IoT.
In this seminar, an overview of the mechanics of thin-ply composites will be presented to highlight the main performance advantages and drawbacks of this new class of composites [1,2].
To explain those mechanisms, a multiscale model of transverse cracking in thin-ply laminates has been developed and provides important insight on the cause of the observed experimental scaling of in-situ strength and apparent toughness of thin-ply quasi-isotropic laminates [3,4].Applications examples on the use of thin-ply composites in aeronautic structures will be presented where a potential weight reduction up to 30% has been demonstrated compared to standard composites while reaching a similar or better production rate by using automation and optimized design for manufacturing.
Finally, the use of thin-ply composites in the manufacturing of smart multifunctional structures will be presented. Acknowledgements: the work presented in this paper is the result of several research projects funded by the Swiss Commission for Technology and Innovation (CTI/Innosuisse), Swiss National Science foundation and HES-SO. The author would like to acknowledge the major contributions of the following people: Robin Amacher, Guillaume Frossard, Sébastien Kohler, Miguel Herraez (EPFL) & B. Giuntoli (HEIG-VD).
About the speaker
After graduating in 2000 as a mechanical engineer with a specialty in solid mechanics, Joël Cugnoni obtained is Ph.D. from EPFL, Switzerland in 2004 in the field of dynamic identification of the elastic properties of composite laminates. After a post-doc in the field of experimental characterization and finite element modeling of micro-electronic solder joints under the supervision of Professor John Botsis, he became senior researcher and lecturer at the EPFL in 2008, were he focused his research on fracture mechanics of composites and multi-scale modeling of complex materials. In 2018, he was appointed associate professor at the University of Applied Sciences of Yverdon-les-Bains (HEIG-VD), Switzerland where he continues his research in composites structure and additive manufacturing.
Brought to you by SASCOM